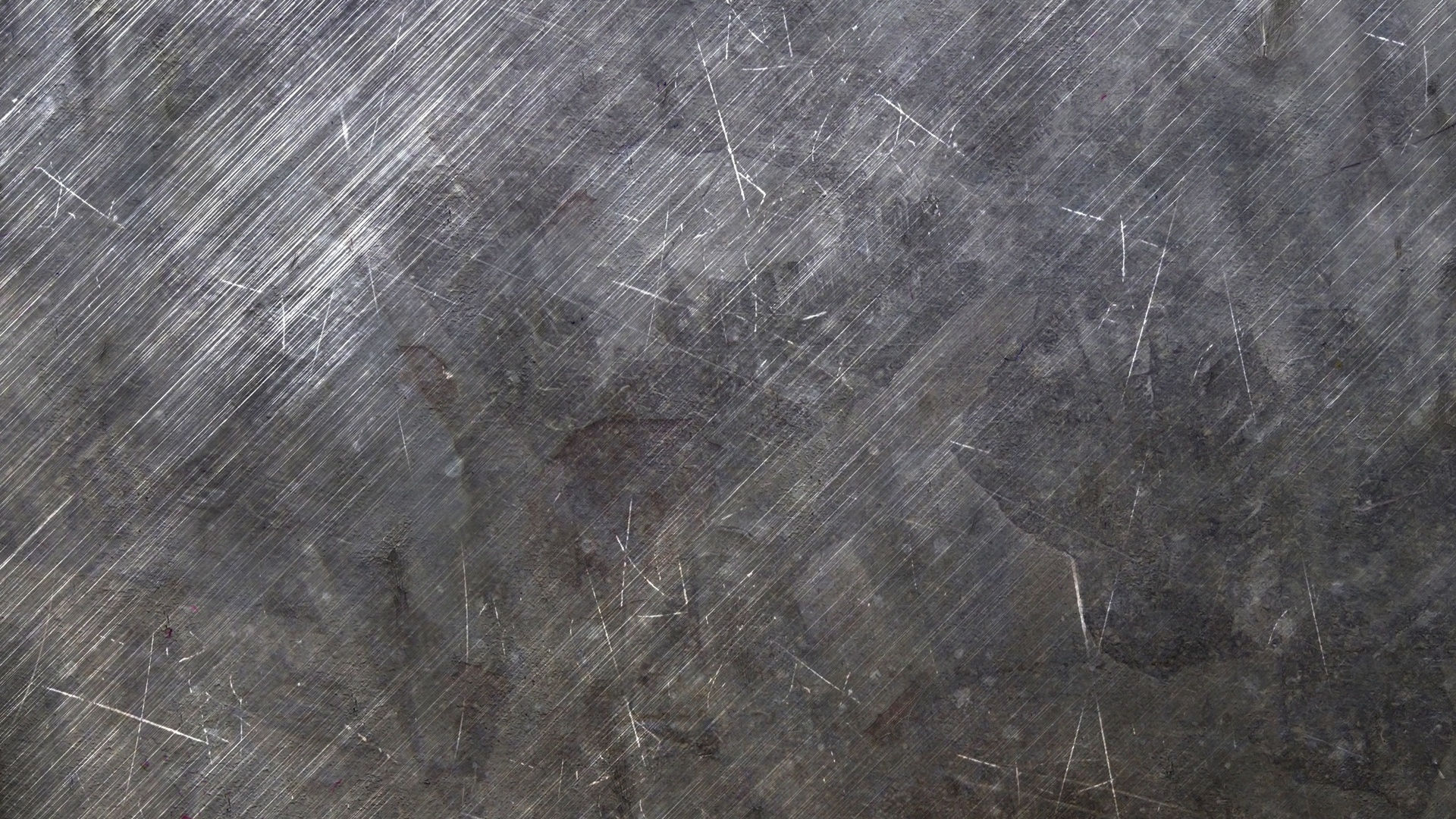
RAZORCLAW
RAZE THE BAR
Construction
Before construction a decision had to be made about which materials to use. Laser cut Perspex was chosen for the gripper, because the design was too complicated to make by hand. But the material for the arm still had to be chosen. The three most important characteristics of the materials for the arm where chosen: easy to fabricate, low weight and strong enough to resist breaking. The material which matched these criteria was wood, because it is light, easy to carve and strong. The connection pieces and other small elements were to be made out of metal, because this is very strong and easy to attach. So a wooden plank was cut into pieces to form the arm out of.
The metal pieces were bought and if needed shaped. And when all parts came together an arm was created
When the pieces of the gripper were finished they were put together and attached to each other. And after the addition of an actuator a working gripper was created.
After having put the arm and gripper together the final product was finished.
A calculation was made to see if the gripper could theoretically lift half a kilo and it should be able to lift it.
Only one thing remained to be done: a name for the gripper. There were a lot of potential ideas for names but one rose above them all: RAZORCLAW. This name describes the function of the gripper perfectly: The claw of the gripper makes almost the same motion as an old fashioned razor. And it didn’t finish there, a slogan was made: Raze the bar. This because the RAZORCLAW literally raises objects and it also figuratively raises the bar for other grippers. And why stop there, even a logo was made for the RAZORCLAW

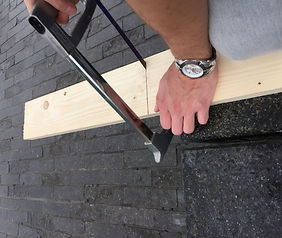
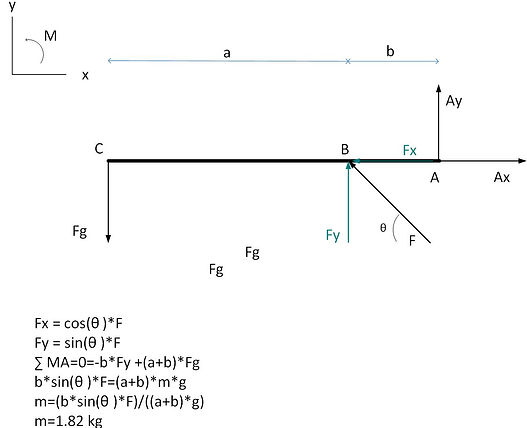